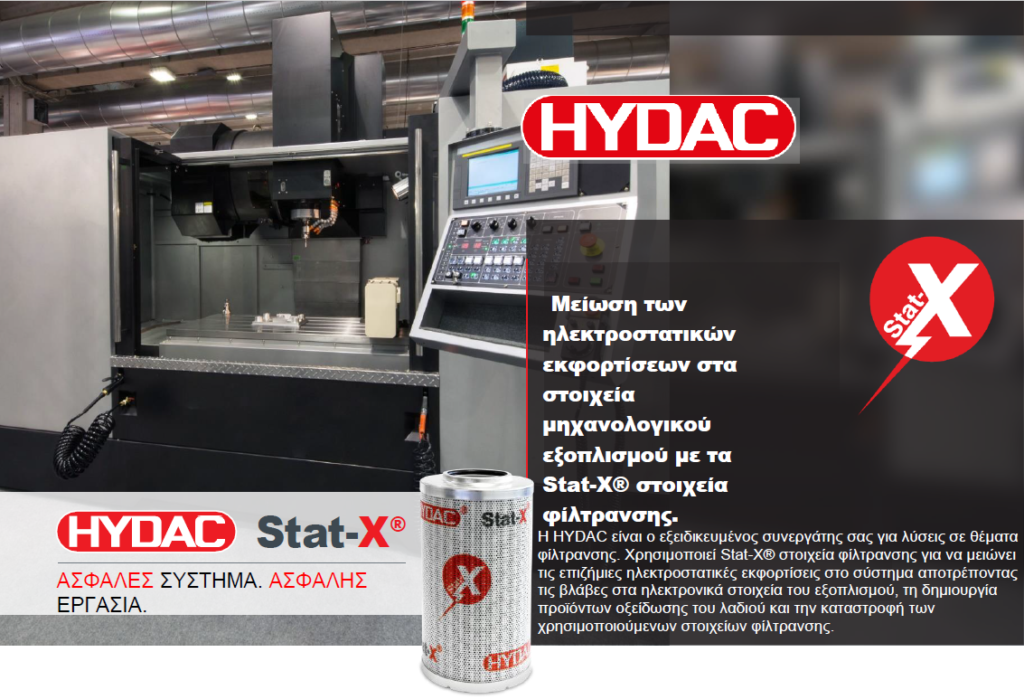
In industry, inexpensive, environmentally friendly and cutting- edge hydraulic oils are being used more and more. These oils are typically zinc-free and ashless and do not contain sulphur. Nowadays, synthetic additives are being used in place of additives containing zinc. The lack of this zinc additive reduces the oil’s conductivity, which can lead to problems in many industrial applications. If a low-conductivity oil flows through a conventional hydraulic or lubricating oil filter element, the fluid can develop a very high electrostatic charge because of the charge separation effects.
If the charge exceeds certain limits, it will abruptly be released in the form of electrostatic discharge. The most obvious form is a spark discharge, which can occur at various locations. If electrostatic discharge occurs in the system, it can cause the following problems:
– Burnt or blocked filter elements
– Increased occurrence of oil degradation products (varnish) and therefore increased component wear and shorter oil change intervals
– Disruption to electronic components
– Deflagration in the tank, burnt breather filters
If discharge occurs outside the system, personal injury can be caused by painful flashovers. The machine safety and occupational safety are impaired and urgent action is required.
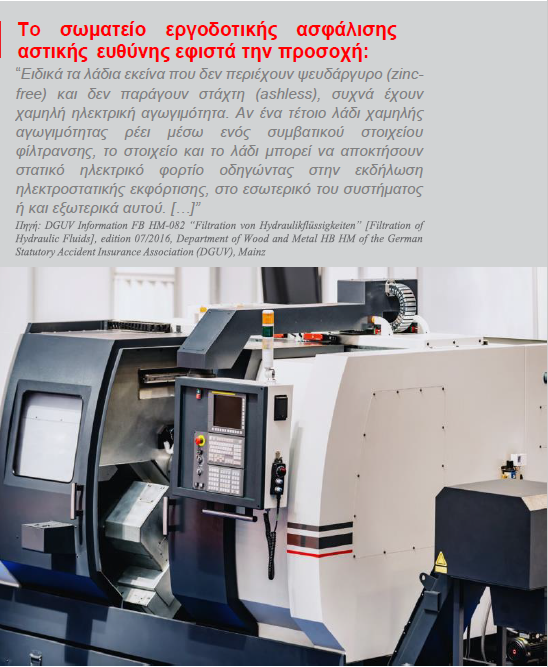
Increase system availability, machine safety and cost optimisation with the HYDAC filter technology approach
Our customer, an international machine tool manufacturer, found that some of their customers were experiencing combustion residues in the oil, destroyed filter elements and in some cases even faults in electronic components installed in the hydraulic system. The customer was already familiar with HYDAC as an expert system partner in hydraulics and contacted us shortly after identifying the problem so that we could find a solution together. The aim was to rectify faults in the electronics and to significantly lengthen the service lives of the hydraulic oil and the filter elements.
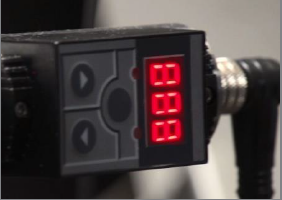
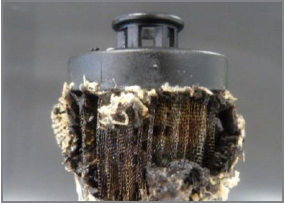
The HYDAC filtration experts and the machine tool industry team analysed the problem on site on the premises of one of the affected machine owners. Measurements, oil analyses and enquiries were carried out. It quickly became clear that the owners were using cutting-edge hydraulic oils with low conductivity in their machine tools and that this was causing the problems. At the HYDAC FluidCareCenter®, further analyses and tests were performed with different oil and filter combinations. This led to the innovative Stat-X® filter element technology. This technology was tested successfully on the end customer’s premises and was able to reduce the electrostatic charging in the system to a minimum. Electrostatic discharge is therefore avoided. The Stat-X® solution is now used in all the manufacturer’s machines.
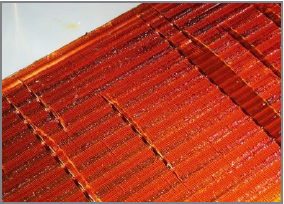
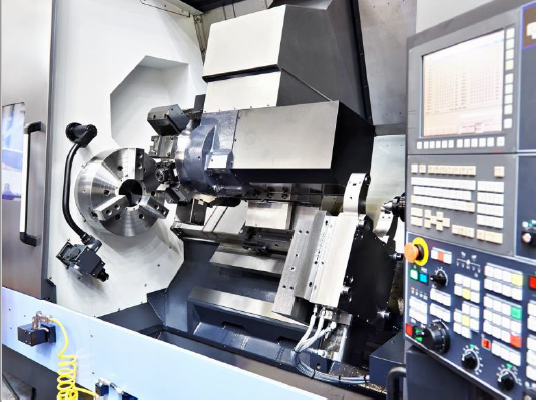
The HYDAC product solution
Stat-X® filter elements to prevent electrostatic charging in highly critical hydraulic and lubrication applications
For many years, HYDAC Filtertechnik has been working to combat electrostatic charging in hydraulic and lubrication systems and to prevent any serious resulting system damage.
With their very special structure and media, the innovative HYDAC Stat-X® elements have been proven to reduce electrostatic charging. As the charge potential is almost zero, sparking is reliably suppressed.
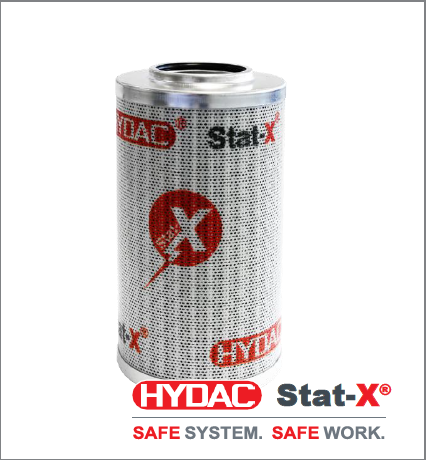
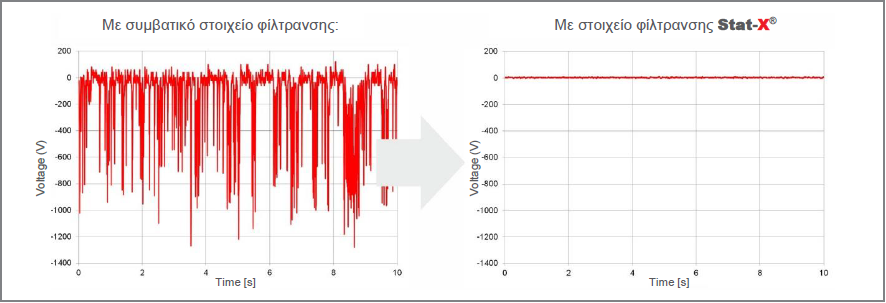
The result
The trend towards modern, low-conductivity oils led our customer to experience electrostatic charging and discharging in the hydraulics of their machine tools. This phenomenon was the cause for damage to filters and components in the system and the increased development of oil degradation symptoms such as varnish. Using Stat-X® filtration technology made it possible to reduce the hazardous charging and discharging in the system while providing excellent ultra-fine filtration.
HYDAC now supplies Stat-X® filters as original equipment in the hydraulic systems of the machine tool manufacturer. Replacing the conventional filter elements with Stat-X® technology also increased the service lives of the hydraulic oil and filters by up to 20% – the systems are still running smoothly to this day.
Your advantages with Stat-X® filter elements
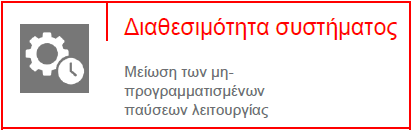
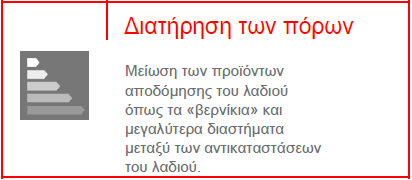
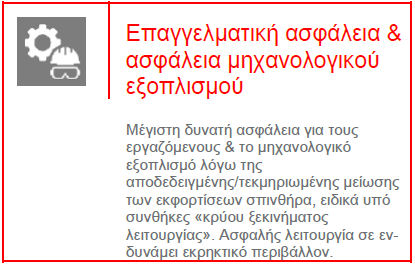
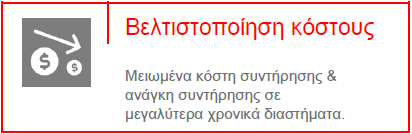
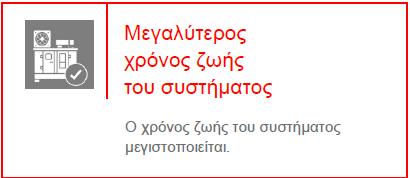
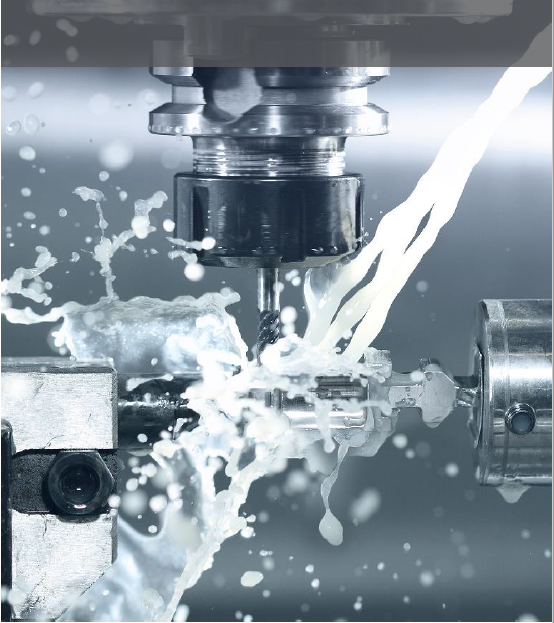